In search of dark energy
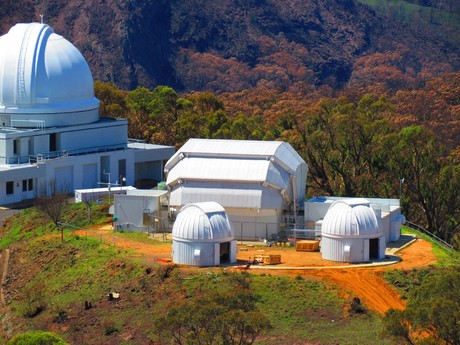
Located on the edge of the picturesque Warrumbungle National Park in New South Wales, Siding Spring Observatory is Australia's premier optical and infrared astronomical observatory with five unique telescopes. They are part of a global network of observatories which allows researchers to track a star in the sky 24 hours per day, seven days per week.
University collaborations allow the observatory to globally facilitate a variety of research, from probing the depths of the cosmos in search of dark energy to searching the Milky Way for other planets and signs of life.
Each telescope is unique, varying in size and capability, with some able to see fainter objects and others able to move faster through the sky, facilitating different observations and new discoveries.
When the back-up power system for one of its largest telescopes was coming to the end of its life, Siding Spring Observatory decided to upgrade its technology.
Protection for all conditions
Mark Willis, Siding Spring Observatory Site Manager, is responsible for maintenance, upgrades and breakdowns at the observatory.
He is tasked with implementing a global maintenance plan which tests equipment and implements necessary upgrades every 18 months. A preventive maintenance plan also ensures the emergency backup system is tested every 12 months. This is to give the team confidence that in the event of power loss, the backup generator will work as intended.
One of the telescopes, a 2-metre equatorially mounted telescope, is much larger than the others. It has a hydraulically operated roof that can open and close multiple times per night. If the roof is open and there is loss of AC mains, there is an emergency backup DC power system complete with batteries that close the roof.
One night, researchers at Siding Spring Observatory opened the roof of the telescope to view the night’s stars. When they were finished, they noticed that the roof of the telescope would not close.
“This really alarmed the researchers at the observatory as any rainfall could cause huge damage to this multimillion-dollar equipment. After some testing, we found that it was the batteries in the backup power system that failed to close the roof of the telescope,” Willis said.
Choosing a reliable partner
Willis was aware that their 48 VDC power backup system was 15 years old and the batteries were nearly due to be replaced. He decided that it was a good opportunity to install a more modern system.
Willis approached Natural Power Solutions as they are a trusted provider of other uninterruptable power supplies (UPS) to the site. Natural Power Solutions recommended that Eaton’s DC power backup system was the best fit for the observatory.
“All of the observatory sites run Eaton AC UPSs globally, so we trust their power systems. Another thing we really value is their backup support. This is what ultimately led us to choose them as our supplier of power backup system,” Willis said.
Eaton’s DC power backup system (48 V) was chosen to back up the emergency hydraulics motor for the telescope.
A local build
This telescope is unique in that it is the only one on this site that needs backup power to the large AC motor that opens and closes it. This is to ensure that in the event of a power outage, the backup DC motor will kick in and ensure the roof can still close.
The DC power backup system that Eaton manufactured works in tandem with a PLC/hydraulic control panel in order to know when to close the roof.
The solution required a lot of intelligence and so configurations were carried out onsite to ensure that the software was configured to know when the roof should open and close, what time it should operate at and when it is fit to operate.
Eaton custom-built the DC power backup system in a couple of weeks and installed it over the course of four days. The system had multiple components including batteries, system SC200 controller, rectifiers and Eaton configured additional features via software which provided safe operation and monitoring.
“Having to get all inputs and outputs done and systems integrated takes a lot of time, but thankfully, Eaton manufactured the DC power system locally and so it only took a couple of weeks to build. This was a key advantage for Eaton as it resulted in a much shorter lead time,” Willis said.
Phone: 02 9693 9333
Adept Cable Drum Trolley and Stand
With manual handling issues a continuing concern on construction sites across Australia, A-frame...
Belden RS485 AWG18 cables
Belden's EN-IEC-rated, low smoke zero halogen (LSZH) RS485 AWG18 cables are designed to...
Remote Control NOJA Power VISI-SWITCH
NOJA Power's VISI-SWITCH, a solid dielectric insulated load break switch with an integrated...